Кварцевые резониторы: основные этапы производства
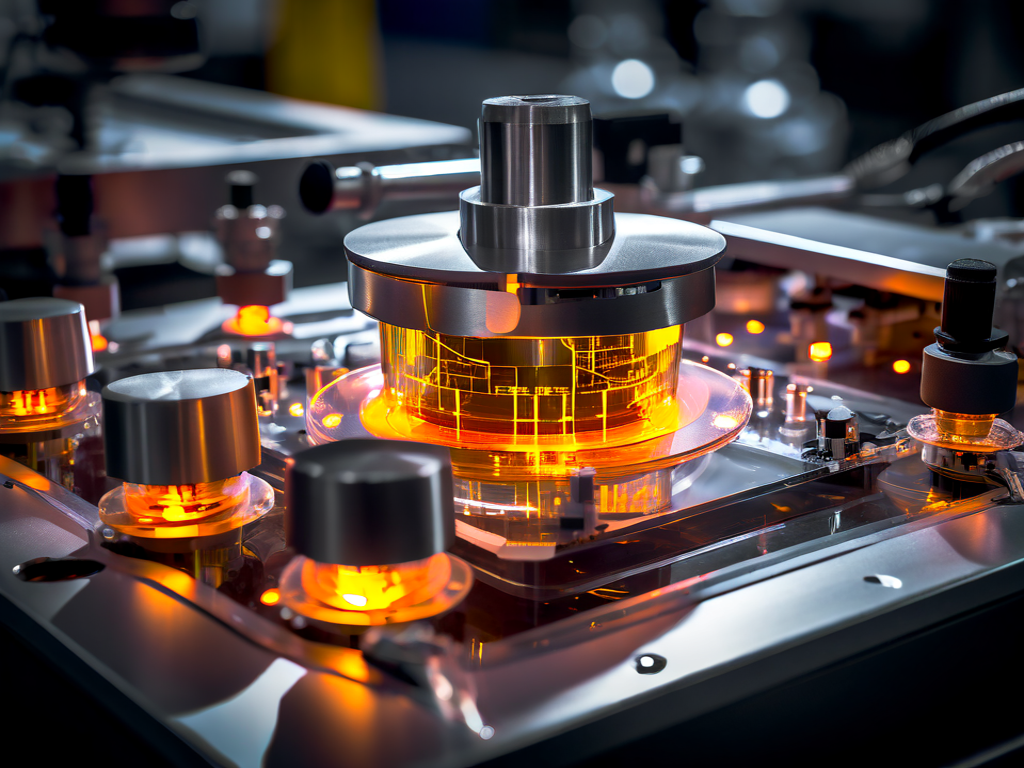
Кварцевый резонатор: технологии производства и контроль качеств
Кварцевые резонаторы: искусство точности в кристалле
Кварцевые резонаторы — незаменимая часть современной электроники, обеспечивающая точность работы множества устройств, от часов и смартфонов до сложных телекоммуникационных систем. Несмотря на компактность и кажущуюся простоту, процесс их производства — это высокотехнологичный путь, в котором каждый этап требует идеальной точности, чистоты и инженерной выверенности. Ниже мы подробно рассмотрим основные стадии изготовления кварцевых резонаторов, каждая из которых скрывает в себе свою порцию технологической красоты.
Выращивание кристаллов кварца: от природной идеи к синтетическому совершенству
Все начинается с самого сердца будущего резонатора — монокристалла кварца. Хотя кварц существует в природе в изобилии, для использования в резонаторах он должен быть исключительно чистым, свободным от примесей и структурных дефектов. Поэтому в производстве применяют синтетически выращенный кварц, получаемый методом гидротермального синтеза.
Этот процесс происходит в специальных автоклавах — герметичных сосудах, где под высоким давлением и температурой воссоздаются условия, близкие к природным. Внутри автоклава размещаются затравочные пластины кварца и кремнезем в растворе на основе щелочи. При температуре около 350–400°C и давлении свыше 1000 атмосфер в течение нескольких недель постепенно формируется кристалл с идеальной кристаллической решеткой.
Кристаллы получают ориентированными строго по осям — Z, X или Y — в зависимости от требуемых характеристик будущего резонатора. Эта ориентация критична, так как именно она определяет частоту и стабильность колебаний. После выращивания кристалл извлекается, тщательно проверяется на наличие микротрещин, включений и отклонений в структуре, ведь малейшая ошибка здесь может свести на нет точность конечного изделия.
Резка и шлифовка: кристалл обретает форму
На следующем этапе крупные монокристаллы превращаются в тонкие пластинки, которые уже напоминают заготовки резонаторов. С помощью высокоточного оборудования из кристалла вырезаются пластины — это один из наиболее критичных этапов. Резка осуществляется по заданной кристаллографической ориентации с точностью до долей градуса.
Используются алмазные круги или лазерная резка, а толщина заготовок может быть менее 0.1 мм. Отклонения в геометрии здесь недопустимы: толщина и форма пластины напрямую влияют на резонансную частоту. После грубой резки следует тонкая механическая и химическая шлифовка. Поверхность должна быть абсолютно гладкой — до атомарного уровня, без микротрещин и заусенцев. Для этого применяются многократные циклы полировки с использованием абразивных паст и ультразвуковой очистки.
Отдельное внимание уделяется контролю ориентации каждой пластины. Даже минимальный сдвиг на доли углового градуса повлияет на рабочие характеристики, а в случае высокочастотных резонаторов может сделать элемент непригодным к использованию. На этом этапе также осуществляется отбраковка: лишь идеальные пластины допускаются к следующей фазе.
Нанесение электродов: создание электрического сердца резонатора
На подготовленные кварцевые пластины наносятся металлические электроды, которые позволяют возбуждать и считывать механические колебания. Обычно используются золото, серебро или алюминий, наносимые методом вакуумного напыления или фотолитографии.
Форма электродов строго задается: чаще всего это круглые или овальные структуры в центре пластины. От размеров и положения электродов зависит активная зона резонатора — та часть, где будут происходить устойчивые колебания. Также часто добавляются "опорные кольца", которые помогают гасить лишние вибрации по краям и стабилизируют частоту.
Кроме самих электродов могут быть нанесены корректирующие слои — например, из оксидов металлов, которые компенсируют температурный дрейф. Такие тонкие инженерные настройки позволяют добиться стабильной работы в широком температурном диапазоне, что критично, например, в авиации или спутниковой технике.
Важно, что нанесение электродов должно происходить в условиях стерильной чистоты, поскольку даже одна пылинка может нарушить симметрию и повлиять на добротность колебательной системы. После нанесения металл проходит процесс отжига, при котором происходит улучшение сцепления с кварцем и снятие внутренних напряжений.
Корпусировка и герметизация: защита точности
Следующим важнейшим этапом становится заключение кварцевой заготовки в защитный корпус. Основная задача — полностью изолировать чувствительный элемент от внешней среды: влаги, пыли, электромагнитных наводок. Классические корпуса изготавливаются из металлов, керамики или стеклокерамики с учетом минимального теплового расширения и высокой герметичности.
Резонатор помещается в корпус на опорные стойки или подвесы. Это должно быть сделано так, чтобы механическое напряжение не искажало колебания. Иногда для минимизации потерь используется вакуумная герметизация или наполнение корпуса инертным газом — например, азотом или аргоном.
Сам процесс герметизации требует высокой точности и контроля: при пайке или лазерной сварке необходимо избежать перегрева, который может повредить кварцевую пластину или изменить ее параметры. В современных производственных линиях герметизация сопровождается автоматизированным контролем качества, включая проверку на утечку (leak test) и контроль резонансной частоты.
Также на этом этапе устанавливаются выводы (выводные ножки или контактные площадки), обеспечивающие подключение резонатора к внешней цепи. Конструкции варьируются: от классических DIP-корпусов до SMD-компонентов размерами менее миллиметра.
Калибровка и тестирование: проверка точности
Перед тем как кварцевый резонатор отправится в электронную схему, он проходит тщательную проверку и калибровку. Измеряются его основные параметры: резонансная частота, добротность, температурная стабильность, эквивалентное сопротивление, уровень фазы шума и другие показатели.
Для этого используются специализированные автоматизированные станции, способные протестировать десятки тысяч резонаторов в сутки. Однако для высокоточных устройств (например, GPS, аэрокосмические приборы, медицинская техника) проводится индивидуальное тестирование, включающее длительные циклы прогрева, охлаждения, вибрационных испытаний.
Калибровка может включать лазерную подстройку: точечным лазером с поверхности удаляется микроскопический слой материала, что позволяет очень точно настроить частоту. Это особенно важно в случаях, когда резонатор должен соответствовать частоте с точностью до долей герца.
После успешного прохождения всех тестов резонаторы упаковываются в антистатические упаковки и маркируются. Каждое изделие получает уникальный код, по которому можно отследить всю историю его производства — от партии кристаллов до температуры пайки корпуса.
Финальная точка — начало точности
Производство кварцевых резонаторов — это удивительное сочетание физики, химии, материаловедения и инженерии. Каждая стадия требует ювелирной точности, и любая мелочь может повлиять на работу всего устройства. При этом спрос на эти миниатюрные элементы только растет — ведь в мире, где все измеряется временем и частотой, стабильность и точность становятся золотым стандартом.
Кварцевый резонатор — это больше, чем кусочек кристалла с двумя электродами. Это сердце точности, заключенное в миниатюрный корпус, несущий в себе сложнейшую работу десятков специалистов, часов кропотливого контроля и мощь науки, доведенной до совершенства.
Производственные технологии кварцевых резонаторов
Основные этапы производства
Производство кварцевых резонаторов включает несколько ключевых этапов, начиная от добычи сырья и заканчивая финальной сборкой и тестированием. Основное внимание уделяется выбору высококачественного кварцевого сырья, которое должно быть очищено от примесей и дефектов. Затем сырье обрабатывается с использованием специализированного оборудования, что позволяет получить кристаллы нужной формы и размера.
Процессы обработки
Обработка кварцевых кристаллов включает в себя резку, шлифовку и полировку. Эти процессы требуют высокой точности, так как даже малейшие отклонения могут повлиять на конечные характеристики резонатора. Используемые технологии могут варьироваться в зависимости от требований к частоте и форме резонатора. Например, в производстве используются как механические, так и лазерные технологии обработки.
Точность и качество кварцевых резонаторов
Важность точности
Точность — один из критически важных факторов при производстве кварцевых резонаторов. Она определяется не только геометрическими параметрами, но и физико-электрическими характеристиками. Небольшие отклонения могут привести к снижению стабильности частоты, что, в свою очередь, негативно скажется на работе конечного устройства.
Методы контроля качества
Контроль качества осуществляется на всех этапах производства. Включает в себя как визуальный осмотр, так и использование высокоточных измерительных приборов для проверки частоты и других параметров. Важно отметить, что на этапе тестирования используются как статические, так и динамические методы, что позволяет более точно оценить характеристики резонаторов.
Калибровка и фильтрация
Процесс калибровки
Калибровка кварцевых резонаторов — это процесс настройки их параметров для достижения максимальной точности. Он включает в себя использование эталонных частот и специализированных программных средств. Калибровка может проводиться как в лабораторных условиях, так и в процессе эксплуатации, что позволяет поддерживать высокую точность на протяжении всего срока службы устройства.
Фильтрация и отбор
Фильтрация резонаторов по их характеристикам осуществляется на основе результатов тестирования. Это позволяет отбирать только те образцы, которые соответствуют установленным стандартам качества. Фильтрация может включать в себя как визуальный отбор, так и использование автоматизированных систем для более точного определения характеристик.
Влияние материалов на качество резонаторов
Выбор материалов
Материалы, используемые для производства кварцевых резонаторов, играют ключевую роль в определении их характеристик. Кварц должен быть высокого качества, без примесей и дефектов. Также важны материалы, используемые для корпуса и других компонентов резонатора, так как они могут влиять на его стабильность и долговечность.
Технологии тестирования материалов
Тестирование материалов включает в себя как физические, так и химические методы анализа. Это позволяет определить, насколько выбранные материалы соответствуют требованиям к качеству и надежности. Использование современных технологий, таких как рентгеновская флуоресценция и спектроскопия, позволяет более точно оценить свойства материалов.
Контроль на всех стадиях производства
Важность контроля
Контроль на всех стадиях производства кварцевых резонаторов необходим для обеспечения их надежности и стабильности. Он включает в себя как внутренний контроль со стороны производителя, так и внешние проверки со стороны независимых организаций. Это позволяет гарантировать, что конечный продукт будет соответствовать всем установленным стандартам.
Стандарты качества
Существуют международные стандарты, регулирующие производство и тестирование кварцевых резонаторов. Они включают в себя требования к точности, стабильности и долговечности. Соблюдение этих стандартов является обязательным для всех производителей, что обеспечивает высокое качество и надежность продукции.
Повышение надежности кварцевых резонаторов
Методы повышения надежности
Повышение надежности кварцевых резонаторов достигается за счет оптимизации производственных процессов, выбора качественных материалов и внедрения современных технологий тестирования. Также важным аспектом является регулярное обновление оборудования и технологий, что позволяет поддерживать высокие стандарты качества на всех этапах производства.
Кварцевые резонаторы — это сложные устройства, требующие высоких стандартов производства и контроля качества. Современные технологии и методы тестирования позволяют достигать высокой точности и надежности, что делает их незаменимыми в различных областях. Инвестиции в качество и технологии производства обеспечивают конкурентоспособность на рынке и удовлетворение потребностей клиентов.