Системы для контроля состояния машин и механизмов: основные принципы
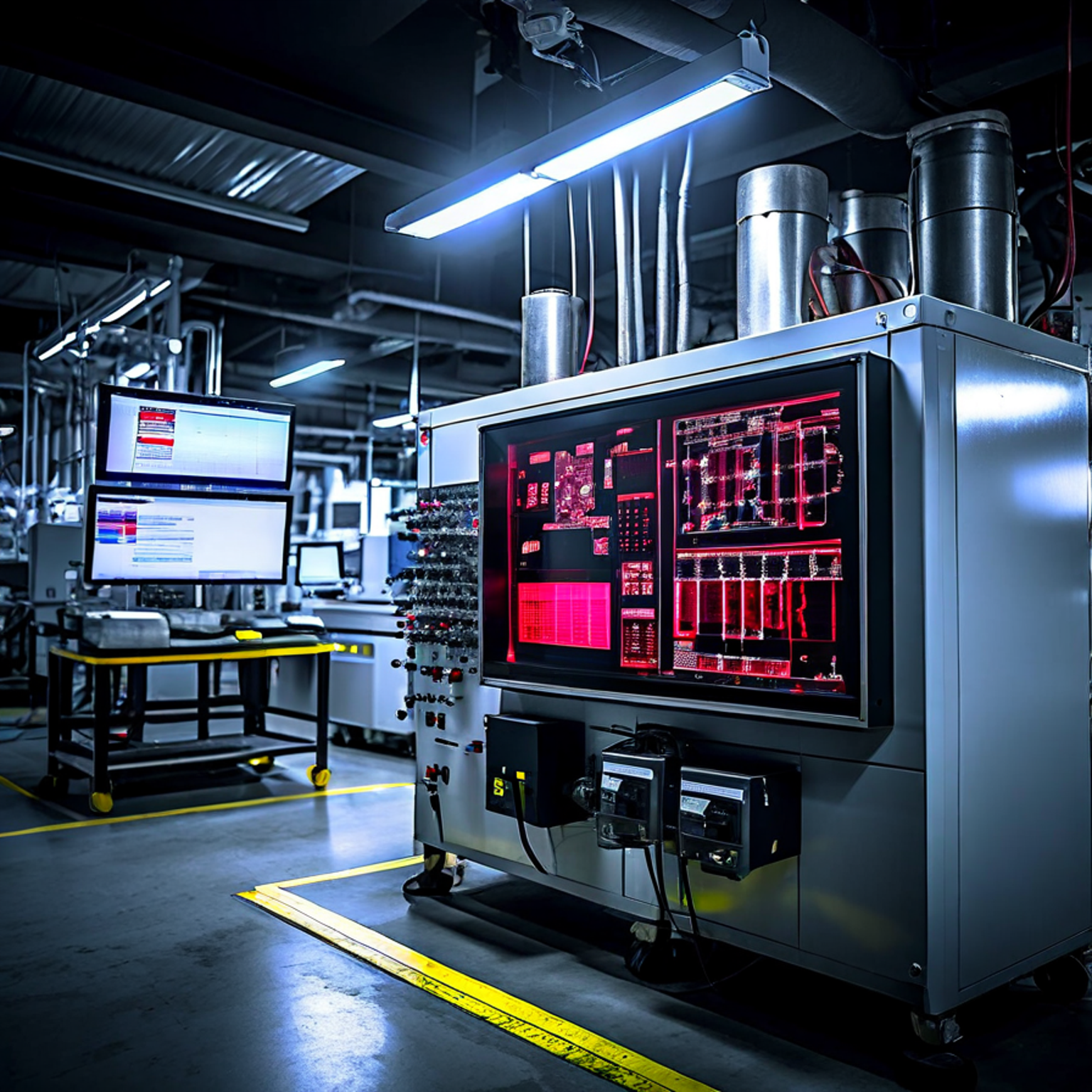
Применение технологий для контроля за состоянием оборудования в промышленных условиях
В современном производстве поддержание оборудования в исправном состоянии является одной из ключевых задач для обеспечения эффективной работы предприятий. Для этого активно применяются различные технологии, позволяющие контролировать состояние машин и механизмов.
Анализ масла и смазочных материалов
По составу и наличию микроскопических металлических частиц в масле можно определить степень износа подшипников и шестерен задолго до поломки.
Контроль вибраций с помощью лазеров
Лазерные интерферометры могут измерять мельчайшие колебания машин и механизмов, позволяя обнаруживать дисбаланс и износ, который еще незаметен стандартными методами.
Оптоволоконные датчики
Встроенные в конструкции, они способны отслеживать изменения температуры, давления и даже механические деформации в трубопроводах, мостах и резервуарах.
Рентгеновская и гамма-томография
Позволяет "просветить" оборудование изнутри и выявить трещины, коррозию или дефекты сварных швов, которые невозможно заметить обычными методами.
Дроны с датчиками и камерами
Используются для осмотра труднодоступных мест, например, трубопроводов, дымовых труб, линий электропередач или ветряных турбин. Они оснащаются тепловизорами, газоанализаторами и даже ультразвуковыми сенсорами.
Биологические сенсоры (бактерии для обнаружения утечек)
Генно-модифицированные микроорганизмы могут реагировать на утечки нефти, газа или токсичных веществ, изменяя цвет или излучая флуоресценцию.
Квантовые сенсоры
Они позволяют измерять мельчайшие магнитные поля и механические изменения, что открывает новые возможности для обнаружения скрытых дефектов.
Эти инновации не только делают промышленность более эффективной, но и позволяют предотвратить аварии, продлить срок службы оборудования и минимизировать риски.
Сенсоры для анализа вибрации
Важность мониторинга вибрации
Вибрация является одним из основных индикаторов состояния машин и оборудования. Изменения в вибрационных характеристиках могут сигнализировать о наличии неисправностей, таких как дисбаланс, неправильная установка или износ деталей. Использование сенсоров для анализа вибрации позволяет оперативно выявлять такие проблемы и принимать меры по их устранению.
Принцип работы вибрационных сенсоров
Современные вибрационные сенсоры работают на основе различных технологий, таких как пьезоэлектрические элементы или MEMS-датчики. Они фиксируют колебания и передают данные на систему мониторинга, где информация обрабатывается и анализируется. Это позволяет не только отслеживать текущее состояние оборудования, но и выявлять тенденции, которые могут указывать на потенциальные проблемы в будущем.
Датчики для мониторинга температуры
Роль температуры в эксплуатации оборудования
Температура является критически важным параметром, который влияет на работу многих промышленных машин. Перегрев может привести к серьезным поломкам и сокращению срока службы оборудования. Поэтому мониторинг температуры является важной частью системы контроля состояния.
Типы датчиков температуры
Существует множество типов датчиков температуры, таких как термопары, термисторы и инфракрасные датчики. Каждый из них имеет свои преимущества и недостатки, что позволяет выбрать наиболее подходящий вариант для конкретного применения. Например, термопары могут использоваться в широком диапазоне температур и подходят для различных условий эксплуатации.
Системы для анализа состояния машин
Комплексный подход к мониторингу
Системы для анализа состояния машин представляют собой комплексные решения, которые объединяют данные от различных сенсоров и датчиков. Это позволяет получить полную картину состояния оборудования и выявить возможные проблемы на ранних стадиях.
Программное обеспечение для анализа данных
Современные системы мониторинга часто оснащены мощным программным обеспечением, которое позволяет не только собирать данные, но и проводить их анализ с использованием алгоритмов машинного обучения. Это позволяет предсказывать возможные поломки и оптимизировать процессы обслуживания.
Системы диагностики
Автоматизация процессов диагностики
Системы диагностики играют важную роль в поддержании работоспособности оборудования. Они позволяют автоматизировать процессы выявления неисправностей и значительно сократить время на их устранение.
Инструменты для диагностики
В современных системах диагностики используются различные инструменты, такие как анализаторы состояния, которые могут проводить комплексные тесты и оценивать состояние оборудования по множеству параметров. Это позволяет быстро и точно определить причину неисправности.
Мониторинг износа деталей
Значение контроля износа
Контроль за износом деталей — это важная часть системы управления техническим обслуживанием. Своевременное выявление изношенных компонентов позволяет избежать серьезных поломок и продлить срок службы оборудования.
Методы мониторинга износа
Существует несколько методов мониторинга износа, включая визуальный осмотр, ультразвуковую диагностику и использование специальных датчиков. Каждый из этих методов имеет свои особенности и может быть применен в зависимости от типа оборудования и условий эксплуатации.
Предсказание поломок
Преимущества предсказательной аналитики
Предсказание поломок — это важный аспект, который позволяет предприятиям минимизировать время простоя и снизить затраты на обслуживание. Использование технологий предсказательной аналитики позволяет заранее выявлять потенциальные проблемы и планировать мероприятия по их устранению.
Алгоритмы и модели предсказания
Современные системы используют различные алгоритмы и модели для предсказания поломок, включая методы машинного обучения и статистического анализа. Эти технологии позволяют обрабатывать большие объемы данных и выявлять скрытые закономерности, которые могут указывать на потенциальные неисправности.
Современные технологии позволяют предсказывать поломки, повышать эффективность производства и снижать затраты на ремонт. Вот самые интересные и необычные методы контроля оборудования:
Предиктивная аналитика и искусственный интеллект
Алгоритмы машинного обучения анализируют данные с датчиков и предсказывают износ деталей задолго до поломки. Например, нейросети могут определить аномальное поведение двигателя по вибрациям и температуре.
Акустическая эмиссия
Специальные датчики улавливают ультразвуковые волны, возникающие при микротрещинах в металле или утечках газа. Эта технология позволяет находить повреждения еще до их визуального появления.
Цифровые двойники
Виртуальная копия реального оборудования собирает данные в режиме реального времени и моделирует поведение машины при разных нагрузках, помогая предсказать возможные сбои.
Беспроводные датчики и IoT
Компактные устройства передают информацию о вибрациях, температуре и давлении по сети, обеспечивая дистанционный контроль без вмешательства человека.
Термография
Тепловизоры выявляют перегрев подшипников, кабелей и соединений, предотвращая короткие замыкания и аварии.
Магнитная томография металлов
Этот метод позволяет обнаруживать внутренние дефекты труб и резервуаров, которые невозможно увидеть обычными способами.
Биомеханические сенсоры для персонала
Устройства отслеживают состояние рабочих и предупреждают о переутомлении, снижая риск аварий из-за человеческого фактора.
Эти технологии делают промышленные предприятия умнее, надежнее и безопаснее, помогая избегать неожиданных поломок и снижать затраты на ремонт.
Внедрение технологий для контроля за состоянием оборудования в промышленных условиях является необходимым шагом для повышения эффективности и надежности производственных процессов. Использование сенсоров для анализа вибрации, мониторинга температуры и диагностики состояния машин позволяет не только предотвратить поломки, но и оптимизировать процессы обслуживания, что в конечном итоге приводит к снижению затрат и увеличению производительности.